Case Studies
With customers in a diverse range of industries around the world, Caplugs provides standard product protection solutions for countless applications.
Beyond the standard, Caplugs engineers closely with customers to create custom parts to suit solve their specific challenges.
Here are some of the product protection challenges customers have faced, and how Caplugs have helped them solve them.
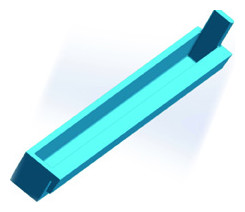
Challenge: An ambitious timeline and a need for a cost-effective solution to make a complex, custom masking solution for a condenser mounting rail. The bar code label on the U-shaped condenser mounting rail must be masked during paint application. It was critical that the bar code remained visible and functional after painting to maintain traceability and control inventory from the plant to the end user. Additionally, the mask needed to stay in place during the painting process.
Solution: Caplugs designed a custom silicone masking insert, with an operator-friendly removal tab to press fit into the mounting rail, and an overhanging lip for extra friction to help hold it in place.
Challenge: An automated microbiology system used in epidemiology studies had two identical openings that needed a tight-fitting closure that could be easily removed. This would allow easy access in the laboratory, ensuring the contents could not spill when the system closed. The plastic plug seals also needed to remain intact when the unit was placed in a centrifuge. Finally, the plugs should be produced under strict cleanliness guidelines and sealed in an easy-open package to prevent direct handling of parts.
Solution: Caplugs designed a custom injection moulded plug that could be easily snapped into place once the test was initiated, ensuring a tight fit. Produced and packaged in an ISO Class 8 cleanroom, the plugs adhered to their stringent cleanliness requirements and were tight enough to ensure the contents would not spill.
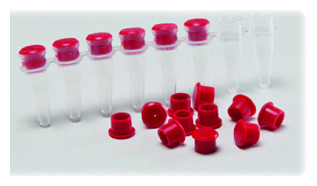
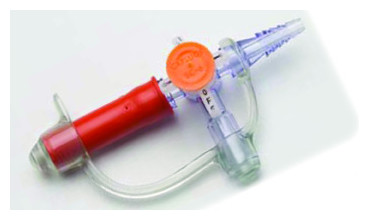
Problem: When suctioning gastric drainage from patients, home healthcare workers sometimes accidentally dropped the port cap of the medical device, causing contamination that could affect the patient or healthcare worker. The customer approached Caplugs, looking to develop a cap with a tether to attach to the valve.
Solution: Caplugs’ engineers developed a unique custom vinyl tether with a two-headed cap that met the functional needs of the clinicians and the homecare patient. The cap fits both ports despite the slightly different diameters, as the vinyl material allows some flexibility. Caplugs also moulded the funnel connector and plug.
Challenge: The customer was using an open vial containing a reagent, with a risk of spillage during secondary processes. They evaluated using various materials, such as covers and plugs, alongside standard protective plugs with little success. Additionally, the customer sought to automate the secondary process of inserting a medium into the vial. Material requirements included gamma stable, non-toxic, Food and Drug Administration (FDA) grade.
Solution: Caplugs engineers designed a custom injection moulded polyvinyl chloride (PVC) plug with shut off. The customer was extremely pleased, noting increased efficiencies and reduced rework.
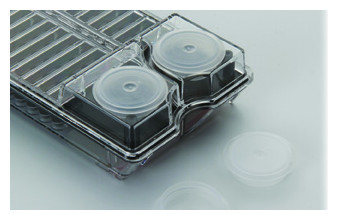