Vinyl dip moulding production
Once the design phase is completed, and the customer has approved the prototype product and selected the materials, production can start. Here is how it works for dip coating and dip moulding.
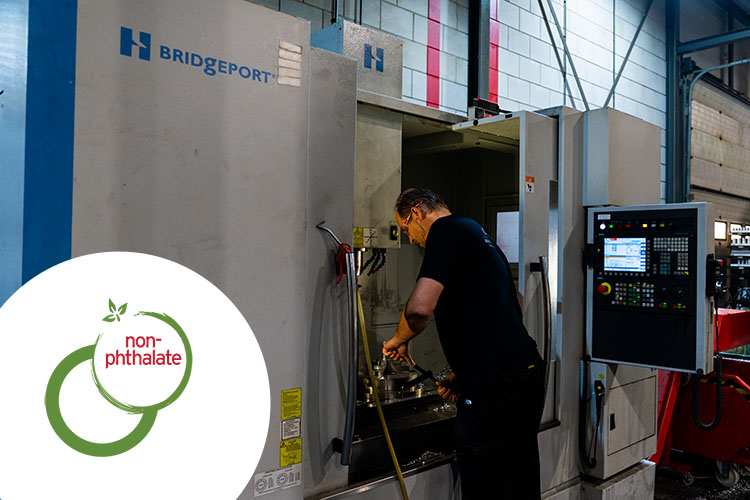
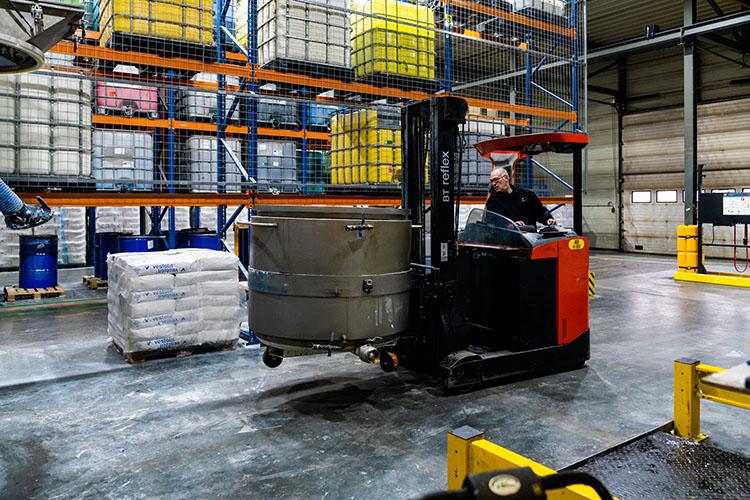
Vinyl dip moulding
In vinyl dip moulding, the liquid PVC is poured into large, heated containers. Aluminium moulds are preheated and then immersed in the liquid mass. The PVC adheres to the dip mould and leaves a thin layer of material on the mould, with the heat of the mould and the dipping time determining the thickness of the plastisol. The mould is then reheated, causing the plastisol to melt and then harden. After this, the formed vinyl can be removed from the mould using compressed air. The vinyl caps and plugs are flexible, so even complex shapes can be easily removed from the dipping moulds.
Vinyl dip coating
With vinyl dip coating, rather than a mould being dipped in the plastisol, the supplied product is dipped whole in the liquid mass and then cured using heat. Dip coating is mainly used to protect materials such as wire grids and racks, but also for things like the handles of tools.
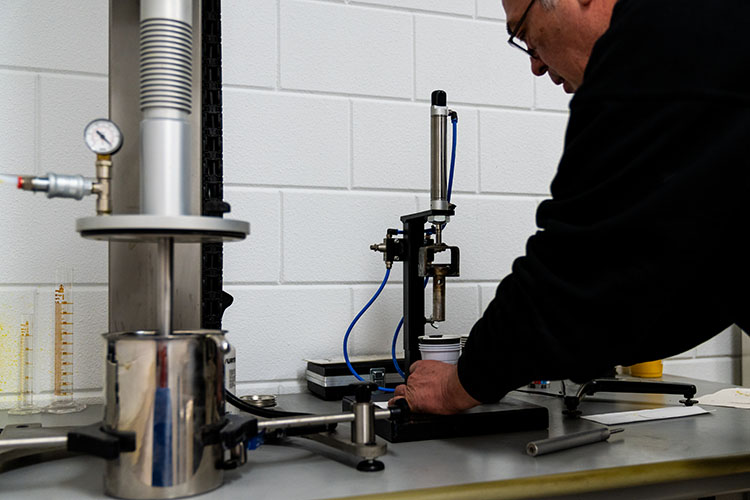
Dip moulding product pricing
The initial production cost is usually significantly lower than the cost of designing a prototype. This is because the settings of the dip moulding process, including dipping speed, dipping time, and temperature of the furnaces, are determined during the prototyping process. When producing large numbers of products, the ideal ratio must be calculated between the number of moulds and the number of dips required to increase the efficiency of the dipping process.
Advantages of the dip moulding process
Vinyl dip moulding and vinyl dip coating eliminate seams and irregularities. In addition, dip moulding is an extremely precise process as the plastisol adheres exactly to the details of the mould. Finally, the possibilities are endless when it comes to colours, textures, thickness, and the final finish of the product, from glossy to matt. It is incredible what shapes can be produced with the vinyl dipping process.
The product is now ready for the final – finishing – stage of the custom vinyl dip moulding process.