Finishing
Once the dip moulding production process is complete, the final step in the production of a custom product begins. This starts with extensive quality control before the product’s durability is tested by bending and pulling the caps and plugs to ensure they do not crack. When products have passed quality control, they go on to one or more finishing processes.
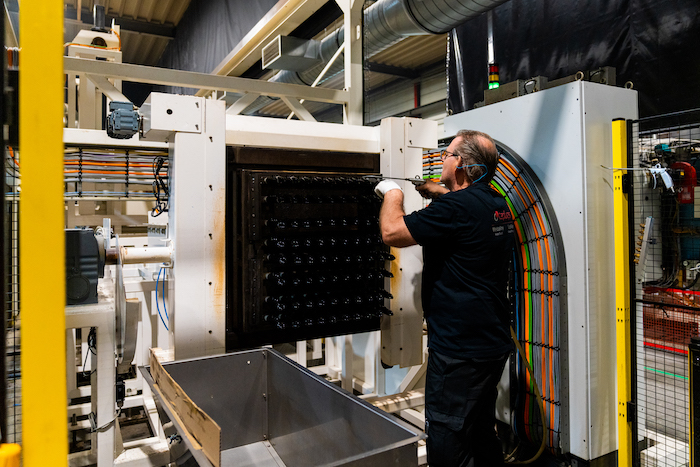
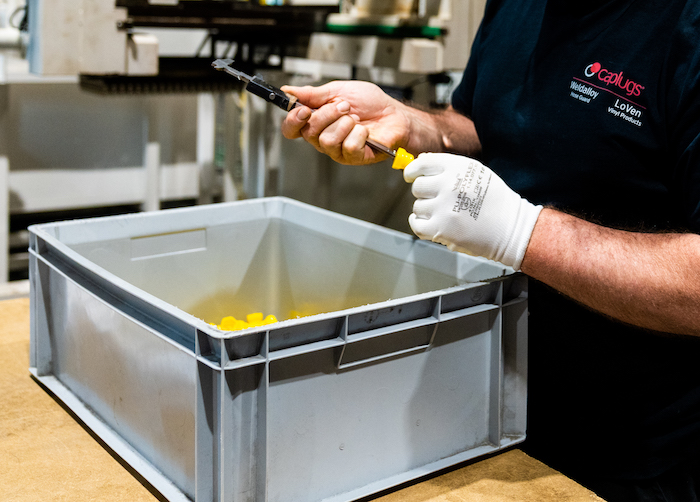
Punching holes
Punching is used to make openings in the product, which can be done with a hand punch or a hydraulic punching machine. The hand punch is used to create holes for electrical cables, such as television cables, which is impossible using the machine. A hole is punched by hand, and the excess plastisol is removed.
Some caps require a ventilation hole. These vinyl caps are pressed onto a nail mat with a mould, which creates these holes. The bolt holes of springs (for instance, shock absorbers under a machine) can also be punched. Vinyl plastisol is put into the holes by dipping, before a hydraulic punching machine puts a bolt into the desired position, which loosens the plastisol and enables its removal.
Punching cut-outs
Some dip moulded products require the removal of certain sections, for example, to ensure that the dip-moulded product can be attached to the item to be protected. It is possible to make cut-outs in various shapes, including rectangles, triangles, circles, zig-zags, and slots.
Sometimes a fitting mould is used, for example, for a fire brigade cutter. Other parts require the finishing points to be incorporated into the dip mould, making it easy to identify the cut-out locations immediately after the dipping process.

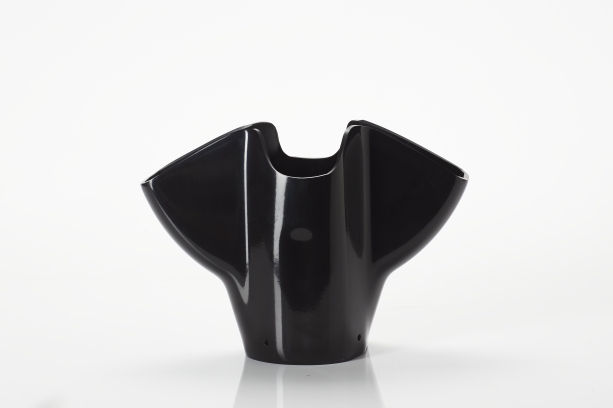
Other treatments
Air bubbles may appear in the plastisol coating during the vinyl coating of springs. To ensure that the metal is no longer exposed, these points are repaired by applying plastisol, which is then heated to 300 degrees so that it cures. Vinyl caps can also be used as sleeves, for example, to protect posts. To make these protective sleeves, the back of the vinyl cap is cut off on a lathe.
Customised packaging and assembly
The vinyl products are packed into bags of 100 pieces using a counting scale. Each customer can specify how they want their products packed with five different packaging sizes available, or provide a crate or pallet for packing and transportation. If required, Caplugs handles the logistics of shipping the products directly to the client’s customers on disposable pallets, saving clients time and money.
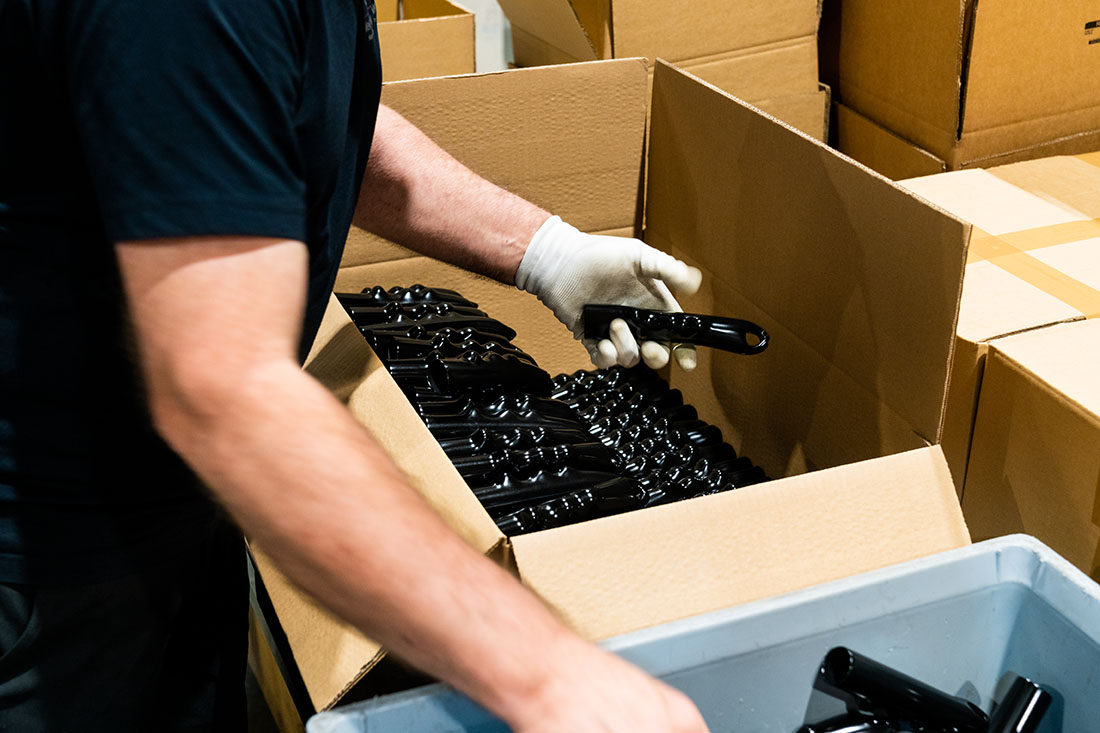