Caplugs uses aluminium moulds to produce standard and custom-made products for dip moulding and injection moulding. This article explains what a mould is and why it is an essential part of the production process for our protective solutions.
A mould is a form that carries a negative or reverse impression of the product to be made. Aluminium is used to get the most detailed shape (geometry) and the exact dimensions for the plastic part to be produced.
Moulds for injection moulding
An injection mould consists of two parts, the injection side and the ejection side. This hollow container is shaped exactly according to the product specifications. The parts are made so that the moulded product can be easily and quickly removed from the mould. In injection moulding, the liquid product material is injected under pressure into the cavity of the injection mould. After the trapped air escapes, the liquid plastic solidifies in the cold cavity and takes the shape of the desired product. After solidifying and removal from the matrix, the product is ready for finishing.
Moulds for dip moulding
Caplugs use a CNC machine to make the aluminium moulds for dip moulding. In dip moulding, unlike injection moulding, the moulds are immersed in liquid vinyl, causing the material to form a layer on the mould. The mould is then heated again briefly to cure the plastisol. After curing, the formed product is blown off the mould with compressed air and is ready for possible finishing.
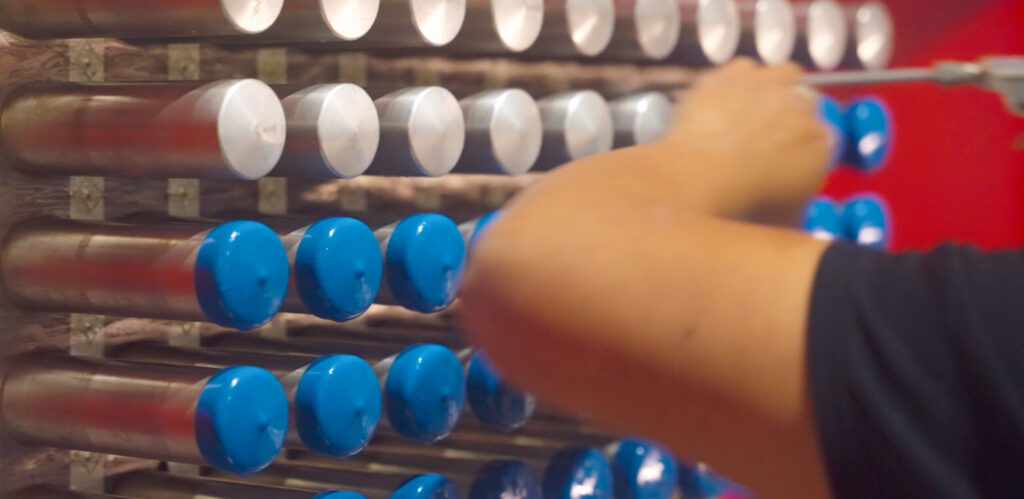
Mould determines geometry and dimensions
The above explanation already makes clear that moulds are essential in the production of vinyl caps and plugs. Caplugs, therefore, pays a lot of attention to making and constantly improving moulds for injection and dip moulding. In addition, much attention is paid to cooling, heating and venting the injection mould, because these aspects determine the quality and purity of the product.
Reuse again and again
Moulds by Caplugs for dip moulding and injection moulding are always thoroughly cleaned after use and inspected for any internal and/or external damage. This is because a clogged or cracked cooling or venting channel or unevenness in the mould surface will have immediate consequences when reused during a subsequent production cycle. Mould reuse applies to standard protection products used in industry, automotive, aviation, aerospace and (petro)chemicals. In addition, Caplugs use so-called multiple moulds. This enables the production of several identical products at the same time during one run.
The perfect mould has its price
Mould making is labour-intensive precision work and a relatively large investment that pays for itself in the long run, which is why Caplugs uses existing moulds wherever possible. The cost of an injection mould is determined, among other things, by the complexity, geometry of the product (part) and the number of products that can be made simultaneously within one injection cycle. Prices for dip moulding and injection moulding moulds vary enormously. For a dip moulding mould, you can expect to pay a few thousand euros, while a mould for injection moulding can go up to €150,000.
Unique moulds for customised protection solutions
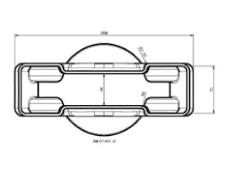
To manufacture custom-made products, Caplugs makes moulds that match customers’ product design and specifications exactly. These moulds are saved for possible future production runs, which means customers do not need to invest again in making new moulds.
The quality of the mould and products are key
Safety during production and the quality of the finished product are always at the heart of Caplugs. Customers must be able to rely on the protection solutions at all times. Would you like more information about products made by injection moulding or dip moulding? Or are you looking for a customised product for your specific application? Then get in touch with the Caplugs team.