In addition to our standard catalogue products, Caplugs offers customers the option of ordering customised dip-moulded caps and plugs for optimised product protection. Using the product to be protected, Caplugs engineers design and create aluminium moulds in the specific shape required. Dip moulding technology is used to make the vinyl protection component for your product. There are a number of options available for the finish of the vinyl caps and plugs.
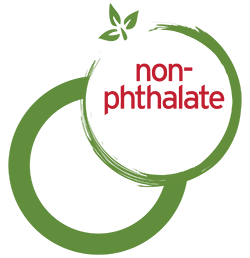
Prototype and design
The first step in the custom dip moulding process is the creation of a prototype for your product.
More about prototyping and design
Materials
Once the design and the product prototype have been approved, the selection of raw materials (vinyl/plastisol) is made. In this stage, the customer can determine the product’s flexibility, colour, and any additional properties.
Find out more about the material choice
Production
After the customer has selected the material, production begins using dip moulding technology.
More about production
Finishing
When the dip moulding process is complete, the products can be finished as required, including punching and cutting. The products are then packed in accordance with customer requirements.
More about finishing
Printing
In addition to dip moulding, it is possible to print a logo or user instructions on custom product protection components.
More about customised printing.