Dip moulding is used to produce many of the protective products in the Caplugs range. This blog post explains which materials are suitable for dip moulding and the advantages of this production method.
The shaping qualities of PVC
As a general rule, dip moulding is only possible with plastics that form well around a mould in liquid form and under high temperatures. Polyvinyl chloride (PVC) is the most commonly used material for dip moulding because it is easy to use and affordable. Other materials frequently used for dip moulding are thermoplastics, such as polythene, polypropylene, polystyrene, polyamide and polycarbonate.
Ideal for protective and masking products
A characteristic of the materials used in dip moulding is that they form a thin skin around the mould like a liquid. At Caplugs, dip moulding uses a plastisol of polyvinyl chloride (vinyl or PVC) beads in a liquid plasticiser. When heated, the vinyl beads absorb the plasticiser, swell and melt into a liquid substance similar to resin. The vinyl plastisol can then be coloured with pigment. Caplugs uses the standard colours black, yellow and red. The aluminium mould used for dip moulding has exactly the shape of the final plastic product. When the mould cools to below 60 °C (140 °F) after dipping, the PVC plastisol cures to a flexible rubbery form. The ready-moulded product is then easily removed from the mould.
Excellent price-quality ratio
The biggest advantage of vinyl dip moulding is the ability to produce large series of vinyl products at a low cost. Depending on the size of the product, several vinyl caps can be made at the same time. There are moulds of three caps, and up to 200 caps can fit on a rack at a time. During the dipping process, the thickness of the material can be adjusted without changing the mould. Even the most complex parts can be easily removed from the mould thanks to plastisol’s elasticity.
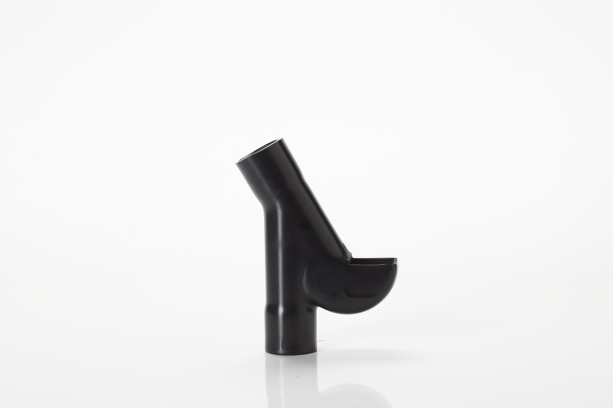
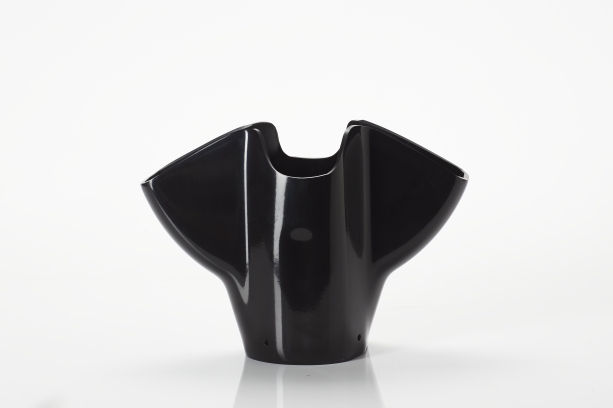
Dip moulding – ideal for product protection solutions
In addition to all the qualities of dip moulding mentioned above, the vinyl plastisol used by Caplugs has a number of other favourable properties:
- Electrical resistance
- Flame retardant
- Noise-reducing
- Chemical and oil-resistant
- Shock and abrasion-resistant
- Corrosion and ultraviolet (UV) radiation-resistant
- Large temperature range from -50°C to +120°C
Caplugs – a specialist in dip and injection moulding products
The standard protection and masking products can be found in the extensive Caplugs catalogue. For a custom-made product for a specific application, please contact us.