Injection moulding is a widely used manufacturing process for producing complex, high-precision components such as the Caplugs plastic product protection solutions. It is an efficient and cost-effective method, making it a popular choice in various industries. This blog post provides a short overview of injection moulding, and provides a step-by-step process for applying an injection-moulded cap.
A short history of injection moulding
Injection moulding is a manufacturing technique that involves injecting molten material, typically thermoplastics, into a mould cavity. The material solidifies inside the cavity to produce the desired shape. It is a highly versatile process used to make plastic products of a precise design and size.
Injection moulding was invented in the 19th century by John Wesley Hyatt, who was searching for a substitute for ivory billiard balls. He discovered that celluloid, a type of plastic, could be moulded into various shapes. This breakthrough paved the way for the development of injection moulding as we know it today.
Injection moulding revolutionised how products were made and is now an integral part of the manufacturing industry.
The importance of injection moulding in manufacturing
Injection moulding plays a critical role in the manufacturing industry for several reasons. It allows for mass production of parts with consistent quality and reduced costs while ensuring product uniformity. This is possible due to automated machinery that can rapidly manufacture significant volumes of components. Producing parts in high volumes is especially beneficial for industries such as automotive, gas and oil, aerospace, construction, electronics, and medical devices.
The process also enables flexible design and the creation of complex shapes with a high level of detail. The mould cavity can be customised to create parts with varying thicknesses, textures, and surface finishes. This versatility allows engineers to design innovative solutions to suit the requirements perfectly.
The exceptional precision, consistency, and accuracy of injection moulding is crucial, especially in industries requiring tight tolerances, such as aerospace and telecommunications.
The fast production cycles of injection moulding enable efficient turnaround times. Once the mould is set up and the initial parameters are established, the injection moulding machine can produce parts at a rapid pace. This efficiency is essential for meeting tight deadlines and meeting consumer demands. Further benefits of the process are laid out in the blog post about the advantages of injection moulding.
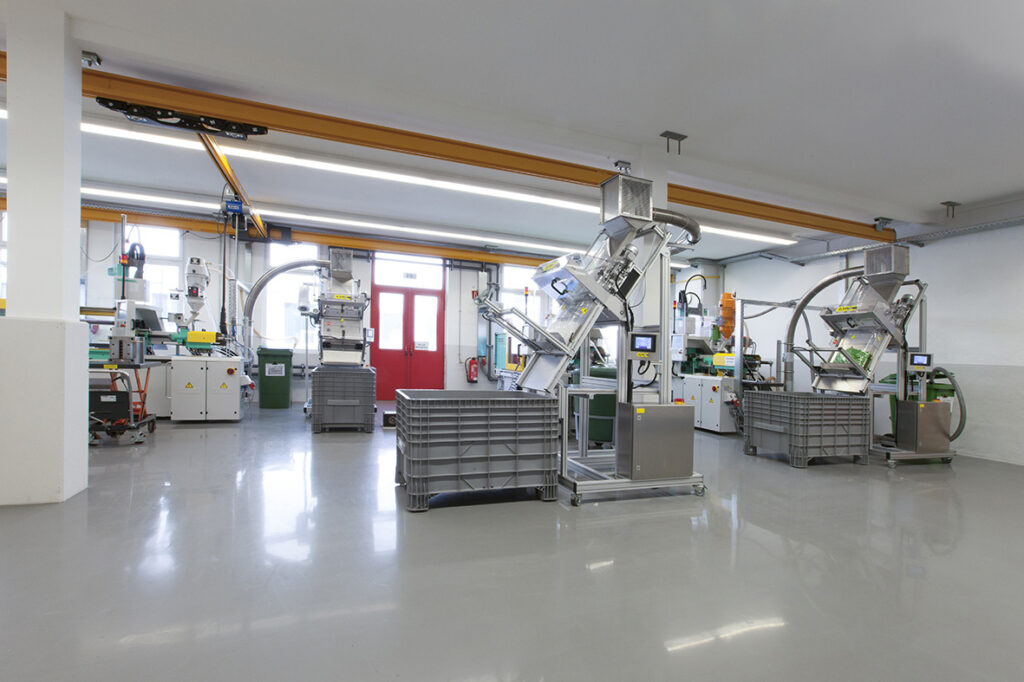
The role of the moulding cap in injection moulding
In injection moulding, the moulding cap keeps the mould secure during injection. It seals and encloses the molten material within the mould, ensuring it solidifies into the desired shape, and averts potential leaks that might cause flaws in the end product. It also regulates material flow, prevents material waste, and enhances accuracy, quality, and efficiency in the injection moulding process. Finally, the smooth surfaces and contours of the moulding cap enable the easy release and ejection of the moulded part from the cavity. This feature enhances productivity and minimises the risk of damage to the part during the ejection process.
Different types of injection moulding caps
Moulding caps come in various types, each designed for specific applications. In order to select the most suitable one for a particular injection moulding project, it is helpful to understand the different types.
- The standard cap is widely used in general injection moulding applications. It offers a good balance of performance, cost-effectiveness, and versatility. Standard caps are available in different sizes and configurations to accommodate various mould designs and material requirements.
- The hot runner cap is used for high-volume production and complex part designs. Hot runner caps feature a heating system that keeps the material in a molten state as it enters the mould cavity. This eliminates the need for re-heating the material with each injection cycle, resulting in faster production cycles and reduced material waste.
- The multi-cavity cap is often used for projects that require multiple cavities, allowing for the simultaneous injection of multiple parts within a single mould. It improves productivity and efficiency by producing multiple components in each injection cycle.
The choice of moulding cap depends on the material used, the desired part design, and production requirements. Selecting the appropriate cap to ensure optimal performance and product quality is crucial.
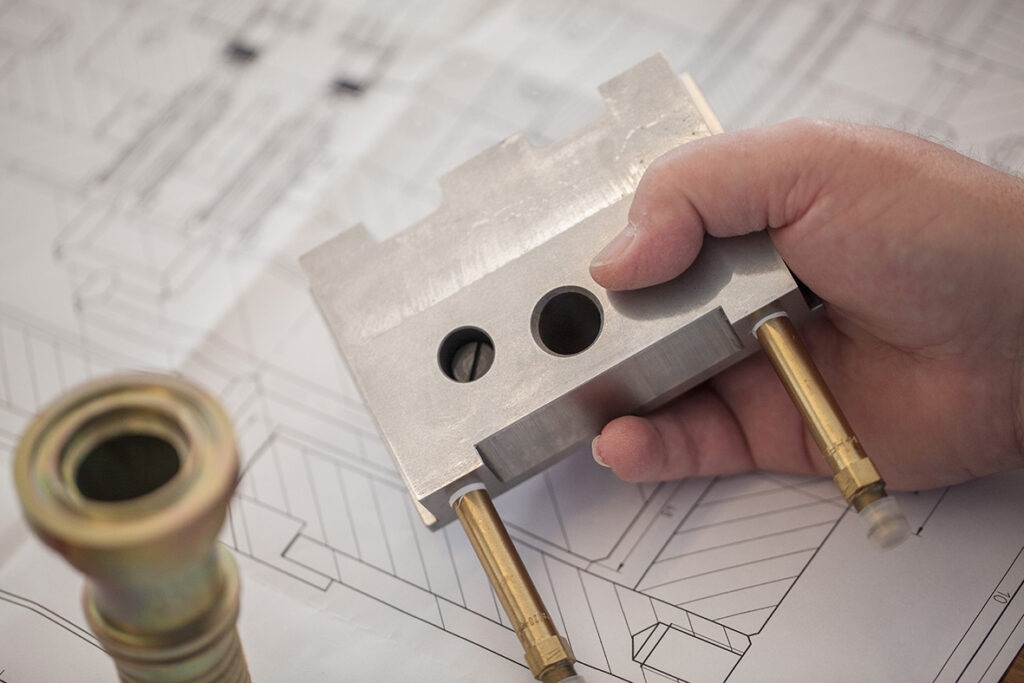
Safety measures for applying the moulded cap
Safety is of the utmost importance when preparing to apply the moulding cap. Make sure to wear suitable protective gear such as gloves and safety goggles to shield against contact with heated materials and moving components. Know the emergency shut-off protocols and keep fire extinguishers easily accessible. Adhere to equipment warning signs and labels, confirm proper ventilation, and assess machinery for signs of wear. These precautions provide a secure environment, minimise accident risks, and facilitate a seamless application of the moulding cap.
Applying a moulded cap
Step 1: Research and preparation
Before starting the cap application, it is important to understand the types and purposes of the caps, as different caps have specific functions. Instructions or guidelines from the manufacturer can be helpful. Samples from the manufacturer also help to physically evaluate the cap’s suitability and size. Collect the tools needed and work in a clean, well-lit space.
Step 2: Clean the part
To ensure a strong bond, begin with a clean surface. Clean the area where the cap will be placed. Dust and dirt hinder adhesion, so use a suitable cleaning solution and a dry cloth. The surface should be completely dry before moving on.
Step 3: Positioning the cap
With the part clean, hold the cap over the designated area, aligning it carefully. Visual indicators or markings guide proper positioning. Double-check to ensure that the cap’s placement matches the product’s intended look and function.
Step 4: Applying the cap
Gently press the cap onto the part’s surface. Start with light pressure to allow adjustments. Gradually increase pressure as the cap adheres, ensuring a secure bond. Avoid excessive force to prevent damage. Follow the manufacturer’s instructions if adhesive is needed.
Step 5: Final check
After applying the cap, inspect it thoroughly. Check the alignment for evenness and symmetry. Look for gaps or irregularities indicating an improper fit. Verify that any locking mechanisms or features are engaged correctly. A meticulous final check ensures a successful application and a finished product that meets expectations.
FAQs
Q: What should I consider before applying a cap to my product?
It is essential to understand the cap’s type and purpose. Different caps serve different functions, so it helps to know the differences in order to select the appropriate cap.
Q: How can I research cap specifications?
The manufacturer’s instructions and guidelines provide information and advice on selecting the correct cap. Samples can be ordered to check the shape, size, and fit of the cap on the product.
Q: Why is cleaning the part necessary?
If the surface of the product is dirty or oily, the cap cannot form a strong bond.
Q: What is the significance of proper positioning?
Visual indicators or markings can indicate proper positioning. This is important to ensure the cap fits well and works as planned.
Q: How should I apply the cap to the part?
Start by gently easing the cap in place using light pressure. Gradually increase the force to achieve a secure fit.
Q: Can I use excessive force when applying the cap?
Avoid using excessive force to prevent damage to the cap or the part underneath. Gradual and controlled pressure is more effective.
Q: What if the cap requires adhesive?
If the cap needs adhesive, follow the manufacturer’s instructions for the correct amount and application method.
Q: Why is a final check important?
A final inspection ensures the cap is properly aligned, there are no irregularities, and any additional features function correctly.
View all the products in our catalogue or contact us for additional information and advice on selecting, ordering and fitting plastic caps.